Welcome to our FAQ page! Here, we have compiled a list of frequently asked questions to provide you with quick and comprehensive answers about Virtual Plant Suite. Whether you are new to our software or a current user seeking clarification, this page is designed to address your queries and help you gain a deeper understanding of our solution.
We understand that adopting new technology can raise questions, and we are here to provide the information you need. Our FAQ page covers a wide range of topics, including the benefits of Virtual Plant Suite, its capabilities, industry applications, integration possibilities, data security measures, pricing structure, and more.
We have carefully curated these frequently asked questions to ensure that you have access to the most relevant and up-to-date information. Our goal is to address any potential concerns or uncertainties you may have, empowering you to make informed decisions about implementing Virtual Plant Suite for your asset lifecycle management needs.
If you can't find the answer you're looking for in our FAQ section, please feel free to reach out to our knowledgeable support team. We are always ready to assist you and provide personalized guidance to ensure you have a successful experience with Virtual Plant Suite.
Browse through our FAQ section below and discover the answers to commonly asked questions. We hope this resource serves as a valuable reference as you explore the world of Virtual Plant Suite and its transformative potential for your organization's asset management.
Please note that the answers provided are for general information purposes. For more specific inquiries or tailored guidance, we encourage you to reach out to our team directly. We appreciate your interest in Virtual Plant Suite and look forward to helping you unlock the full potential of your asset lifecycle management.
Talk to an Expert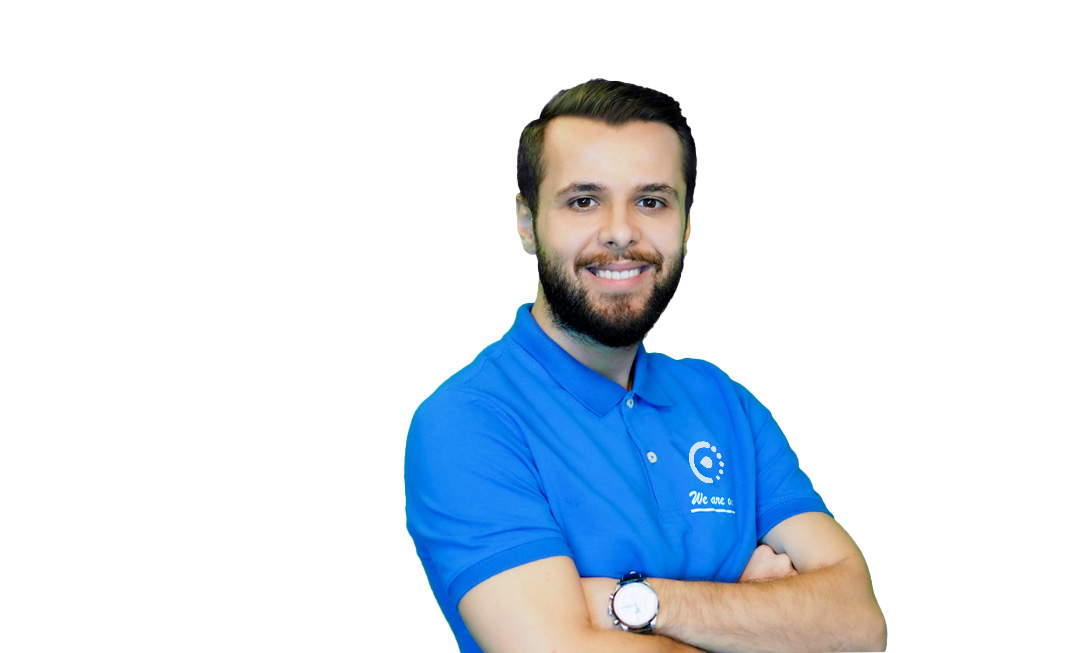
What is Virtual Plant Suite?
Virtual Plant Suite is a comprehensive software solution that enables digital asset management, visualization, collaboration, and data integration. It helps organizations optimize their asset-intensive operations, improve maintenance efficiency, and maximize asset performance.
How can Virtual Plant Suite benefit my organization?
Virtual Plant Suite offers numerous benefits, including enhanced asset visibility and control, streamlined operations, improved maintenance effectiveness, cost savings, improved compliance, and enhanced collaboration and decision-making.
Which industries can benefit from Virtual Plant Suite?
Virtual Plant Suite is designed to cater to asset-intensive sectors such as oil and gas, chemical, petrochemical, fertilizer, biofuels, power and utilities, food and beverage, mining and metals, buildings, and manufacturing.
What is a digital twin, and how does it relate to Virtual Plant Suite?
A digital twin is a virtual replica of a physical asset or system that mirrors its real-world behavior and characteristics. Virtual Plant Suite leverages digital twin technology to create a digital representation of assets, enabling accurate visualization, analysis, and optimization.
Can Virtual Plant Suite integrate with our existing systems and data sources?
Yes, Virtual Plant Suite is designed to integrate seamlessly with various existing systems and data sources, including asset management systems, ERP, IoT devices, sensors, SCADA systems, and more. This ensures comprehensive data integration and enhances the accuracy and value of asset information.
What types of assets can be managed with Virtual Plant Suite?
Virtual Plant Suite can manage a wide range of asset types, including but not limited to process equipment, pipelines, storage tanks, buildings, machinery, and infrastructure.
How does Virtual Plant Suite enhance asset visibility and control?
Virtual Plant Suite provides a centralized platform for storing and managing asset information, enabling real-time visibility and control over asset performance, maintenance activities, and documentation. This helps optimize decision-making and enhances operational efficiency.
Does Virtual Plant Suite support remote collaboration among team members?
Yes, Virtual Plant Suite facilitates remote collaboration by providing a cloud-based platform where team members, contractors, and stakeholders can access and share asset information, collaborate on projects, and make informed decisions irrespective of their location.
What are the cost-saving benefits of using Virtual Plant Suite?
Virtual Plant Suite offers substantial cost savings by optimizing maintenance schedules, reducing downtime, improving resource efficiency, and minimizing operational expenses. Customers have achieved cost reductions ranging from 10% to 25% in maintenance and operational costs.
Is Virtual Plant Suite a cloud-based solution?
Yes, Virtual Plant Suite is a cloud-based software solution that provides the flexibility of accessing and managing asset information securely from anywhere with an internet connection. However, it can also be deployed on-premises if preferred.
How does Virtual Plant Suite ensure data security and privacy?
Virtual Plant Suite prioritizes data security and follows industry best practices. It employs advanced encryption, access controls, and secure cloud-based storage Microsoft Azure to protect sensitive asset information, ensuring data security and privacy.
Can Virtual Plant Suite integrate with other software solutions we use?
Yes, Virtual Plant Suite is designed to integrate with a wide range of software solutions, including enterprise resource planning (ERP) systems, computerized maintenance management systems (CMMS), and other relevant tools, to facilitate seamless data exchange and interoperability.
Does Virtual Plant Suite support mobile access?
Yes, Virtual Plant Suite offers mobile access through responsive web design or dedicated mobile applications. This allows users to access asset information, collaborate, and make informed, decisions on-the-go using their smartphones or tablets.
Can Virtual Plant Suite handle large-scale and complex asset portfolios?
Yes, Virtual Plant Suite is built to handle large-scale and complex asset portfolios. Its scalable architecture and robust data management capabilities enable efficient management and visualization of extensive asset databases.
How long does it take to implement Virtual Plant Suite?
The implementation timeline for Virtual Plant Suite depends on various factors, such as the size and complexity of your asset portfolio, data availability, and customization requirements. Our implementation team will work closely with you to ensure a smooth and efficient implementation process.
Does Virtual Plant Suite offer training and support for users?
Yes, Virtual Plant Suite provides comprehensive training and support to users. We offer onboarding sessions, user documentation, and ongoing technical support to ensure users can effectively utilize the software and maximize its benefits.
How does Virtual Plant Suite facilitate compliance with industry regulations?
Virtual Plant Suite helps facilitate compliance by providing accurate and up-to-date asset information, maintenance records, and documentation. It enables efficient data management and reporting, making it easier to meet regulatory requirements and maintain compliance.
Can Virtual Plant Suite be customized to fit our specific business needs?
Yes, Virtual Plant Suite can be customized to align with your specific business needs and requirements. Our team will work closely with you to understand your unique challenges and tailor the software to meet your specific asset management goals.
What is the pricing structure for Virtual Plant Suite?
The pricing structure for Virtual Plant Suite varies based on factors such as the scope of implementation, asset portfolio size, and additional customization requirements. Please contact our sales team for detailed pricing information tailored to your specific needs.
Can Virtual Plant Suite be used for both new and existing assets?
Yes, Virtual Plant Suite can be used for both new assets and existing assets. It supports the entire asset lifecycle, including design, construction, operations, maintenance, and decommissioning.
How does Virtual Plant Suite contribute to sustainability and ESG goals?
Virtual Plant Suite contributes to sustainability and Environmental, Social, and Corporate Governance (ESG) goals by optimizing maintenance activities, reducing energy waste, improving resource efficiency, and minimizing carbon footprint. This helps organizations meet their sustainability targets and enhance their ESG performance.
What are the future developments and updates planned for Virtual Plant Suite?
We are committed to continuous improvement and innovation. Our development roadmap includes regular software updates, new features, and enhancements based on customer feedback and emerging industry trends. We prioritize staying at the forefront of technology to meet the evolving needs of asset-intensive industries.